Nano-Robot . Atomic Force Microscopy Imaging (Miss Ebrahimi) For doing a manipulation process and understanding the topography and mechanical properties of samples, one proper device is the atomic force microscopy (AFM). AFM is one member of scanning-probe microscopies (SPM). It is composed of a microcantilever, sensing and control system and an exciter. Atomic force microscopy (AFM) has been extensively used to study the surface topography of a wide variety of materials and to measure intramolecular forces . An optical detection technique is often used to monitor the amplitude of oscillation, frequency, and phase of the AFM cantilever. During scanning, a particular operating parameter such as amplitude is maintained constant, and images are generated using a feedback loop between the optical detection system and the piezoelectric scanners. To produce topographic images of a sample, contact mode, non-contact mode, and tapping mode can be used. Tapping mode AFM offers advantages in surface topography measurements when compared to contact and non-contact modes. - Related projects:
- Dynamics of TMAFM in air
- Dynamics of TMAFM in liquid
- Dynamics of TMAFM with carbon nanotube tip in air
- Dynamics of TMAFM with carbon nanotube tip in liquid
. Atomic Force Microscope Based Nanomanipulation (Miss Zakeri) It is nanoparticle positioning system using Atomic Force Microscopes (AFM). As a definition of the pushing process of a particle, the tip of the AFM probe approaches the target particle and makes contact with it. To be sure of the contact between the tip and nanoparticle, an initial normal deflection, must be indicated in the cantilever. At the beginning of the pushing process, both the substrate and the particle are stationary. Then, the substrate starts to move with a constant velocity, and the adhered particle moves with the substrate. The lateral movement of the particle, which is in contact with the tip, helps increase the interaction force, the so called pushing force. Finally, the pushing force reaches a critical value, necessary for overcoming the adhesion force between the particle and substrate. At this moment, which is denoted as the critical time of pushing, the tip stops the particle against the substrate, and the particle starts to move relative to the substrate, and consequently, the nanoparticle rolls or slides on the substrate. Related projects: - Dynamic modeling of manipulation of micro/nanoparticles on rough surfaces
- Dynamic Modeling of Nanoparticle Pushing Based on V-Shape Cantilevered AFM
- Sensitivity analysis of the manipulation process
- Dynamic Modeling of Nanoparticle Pushing in liquid environment
- Simulation of particles manipulationbased on the accurate friction models in the nano-scale (Mr.Taheri)
. Multi-scale modeling of Nano robots The linking of our macroscopic world to the nanoscopic world of single molecules, nano-particles and functional nanostructures is a technological challenge. Especially in the nano-manipulation process, piezoelectric sensors and actuators are essential parts of nano-robotic systems. In scanning probe microscopes (SPM), especially atomic force microscope (AFM), a piezotube is used to move the stage in space directly. A micro cantilever is used to sense or actuate partially the stage. We used a multi-scale method to model the combined behavior of nano-manipulation. Some deformations of particle in various states are introduced bellow. Tip damage is one of the causes of unsuccessful nano-manipulation process. This phenomenon leads to the formation of crack in the tip, permanent deformation of the tip end, or even in some cases, the fracture of the tip. 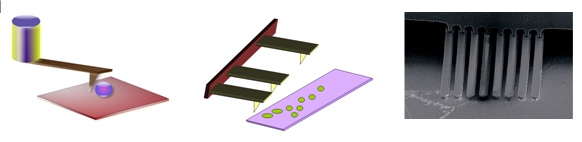
Modeling of macro-micro parts Modeling of micro-nano parts Nonlinearities of macro-micro parts Nonlinearities of micro-nano parts
|